Rotor Aeroacoustics

Development of noise prediction models
At the Institute of Aerodynamics and Gas Dynamics (IAG) different models for the efficient determination of trailing edge noise have been developed (Xnoise, XEnoise and Rnoise). Numerical prediction results are extensively validated with measurement data obtained in institute’s Laminar Wind Tunnel (LWT), and excellent agreement has been observed. This qualifies the developed methods for the analysis and design of quiet airfoils. The enhanced prediction schemes are coupled in a Graphical User Interface (GUI) based tool IAGNoise.
IAGNoise has been extended for 3D applications as well. The model consists of dividing the blades of the wind turbine into two-dimensional airfoil sections and predicting the total noise emission as the sum of the contribution from each blade element for a given observer position under consideration of Doppler effects.
Noise reduction
Acoustic design and wind tunnel measurement of airfoils
Noise emission is one of the major obstacles for a further spread of on-shore wind turbines and significantly limits public acceptance. Tightened noise regulations force the wind turbine manufacturers to make serious efforts in noise reduction. The flow-induced noise emitted from the blades is complex to comprehend and to reduce and, therefore, represents the current focus for further noise reduction.
Investigations including field tests suggest that the trailing edge noise is the most dominant noise source of modern wind turbines. This particular noise basically stems from an interaction of the turbulent eddies within the boundary layer and the associated pressure fluctuations with the trailing-edge of the rotor blades. Because the state of the turbulence in the vicinity of the trailing edge is determined by the development of the boundary layer and thus by the shape of the pressure distribution along the blade section, noise emission can be influenced and finally reduced by an adequate design of the airfoil. The objective is to reduce the noise emission and increase aerodynamic performance at the same time.

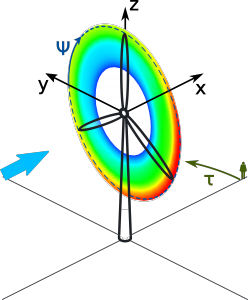
Acoustic assessment of airfoils and rotors
Trailing edge noise remains the most dominant noise source of modern wind turbines. This particular noise basically stems from an interaction of the turbulent eddies within the boundary layer and the associated pressure fluctuations with the trailing-edge of the rotor blades.
Because the state of the turbulence in the vicinity of the trailing edge is determined by the development of the boundary layer and thus by the shape of the pressure distribution along the blade section, it is obvious that the noise emission is influenced by the design of the rotor airfoil. Based on substantial experience in aerodynamics and aeroacoustics the IAG analyses airfoils using in-house noise prediction codes with regard to the identification of potential noise sources and their reduction.
Numerical simulation and wind tunnel testing of passive and active means for noise reduction
IAG investigates the effects of passive and active devices for the reduction of flow induced noise of wind turbine rotor blades. The achieved noise reduction can increase the acceptance of on-shore wind turbines or it can be used to improve the performance of the wind turbine by increasing the rotation speed of the rotor.
The institute’s investigations focus on a reduction of the trailing edge noise by passive (airfoils design, trailing edge modifications) and active (suction, blowing) means. Among other things it was shown that a distributed suction of the boundary layer leads to a significant noise reduction. At the IAG both numerical and experimental investigations about noise reduction are performed.• ActiQuiet (active noise reduction of wind turbines)
- ActiQuiet (Active noise reduction of wind turbines)
- INFLOW-Noise (Numerical and experimental studies on inflow and trailing-edge noise of wind turbines)
- IEA Annex MexNext III (Validation of aerodynamic and aeroacoustic codes for wind turbines)